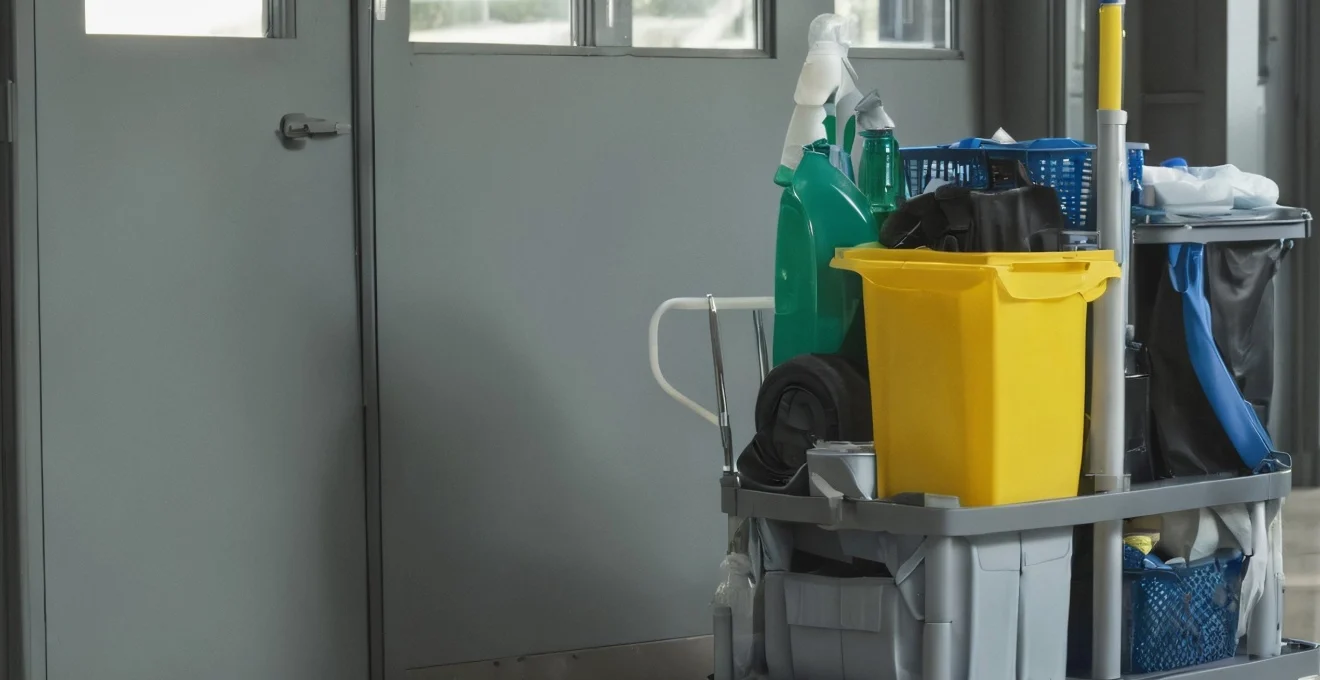
In the world of commercial cleaning, having the right equipment and supplies is crucial for maintaining pristine, hygienic environments. Whether you're managing a large office complex, a bustling retail space, or a healthcare facility, the tools and products you use can make a significant difference in the efficiency and effectiveness of your cleaning operations. This comprehensive guide explores the essential equipment, supplies, and technologies that form the backbone of successful commercial cleaning services.
High-performance cleaning equipment for commercial spaces
The foundation of any professional cleaning operation lies in its equipment. High-performance machines not only increase efficiency but also ensure thorough cleaning that meets the stringent standards of commercial environments. Let's delve into the key categories of cleaning equipment that are indispensable for commercial cleaning professionals.
Industrial-grade vacuum cleaners: HEPA filtration and backpack models
Industrial-grade vacuum cleaners are the workhorses of commercial cleaning. These powerful machines are designed to handle large areas and heavy foot traffic. HEPA (High-Efficiency Particulate Air) filtration systems are particularly important, as they capture 99.97% of particles as small as 0.3 microns, ensuring excellent air quality.
Backpack vacuum models offer superior mobility and ergonomics, allowing cleaners to navigate tight spaces and staircases with ease. These units typically weigh between 10-15 pounds and feature padded harnesses for comfort during extended use. The efficiency gain from backpack models can be significant, with some studies suggesting up to a 230% increase in productivity compared to traditional upright vacuums.
Commercial floor scrubbers and burnishers: rotary vs. orbital technology
Floor scrubbers and burnishers are essential for maintaining hard floor surfaces in commercial settings. Rotary machines use circular motion and high speeds to clean and polish floors, while orbital technology employs a random orbital action that can be more effective for deep cleaning and stripping.
Rotary burnishers typically operate at speeds between 1000-3000 RPM, creating a high-gloss finish on floors. Orbital machines, on the other hand, often run at lower speeds (around 1400-1600 RPM) but can provide more consistent coverage and are less likely to leave swirl marks. The choice between rotary and orbital technology often depends on the specific flooring material and desired finish.
Carpet extractors: hot water vs. dry cleaning systems
Carpet extractors are crucial for maintaining carpeted areas in commercial spaces. Hot water extraction systems, also known as steam cleaning, use a combination of hot water and cleaning solution to deep clean carpets. These machines typically heat water to temperatures between 140-220°F, which helps to break down dirt and stains effectively.
Dry cleaning systems, on the other hand, use minimal moisture and rely on specialized cleaning compounds to lift dirt from carpet fibers. These systems have the advantage of faster drying times, often allowing carpets to be walked on within 30 minutes to an hour after cleaning.
Pressure washers: electric vs. Gas-Powered options for exterior cleaning
Pressure washers are indispensable for exterior cleaning tasks such as building facades, sidewalks, and parking areas. Electric pressure washers are typically quieter and more suitable for indoor use or areas with strict noise regulations. They generally produce pressures ranging from 1300-1900 PSI, which is sufficient for most commercial cleaning tasks.
Gas-powered pressure washers offer greater mobility and higher pressure outputs, often exceeding 3000 PSI. These are ideal for large outdoor areas or heavy-duty cleaning jobs. However, they require more maintenance and produce emissions, making them less suitable for indoor use or environmentally sensitive areas.
Essential cleaning supplies and chemicals for professional results
While high-performance equipment forms the backbone of commercial cleaning operations, the right cleaning supplies and chemicals are equally important for achieving professional results. Let's explore the essential products that should be in every commercial cleaner's arsenal.
All-purpose cleaners: pH-Neutral vs. alkaline formulations
All-purpose cleaners are versatile products that can handle a wide range of cleaning tasks. pH-neutral formulations are gentle on surfaces and safe for use on most materials. They typically have a pH between 6 and 8, making them ideal for daily cleaning of surfaces like countertops, glass, and lightly soiled areas.
Alkaline cleaners, with a pH above 7, are more effective at breaking down grease and heavy soil. These are particularly useful in kitchens, industrial settings, or areas with stubborn dirt. However, care must be taken when using alkaline cleaners on sensitive surfaces, as they can cause damage if not used properly.
Disinfectants: EPA-Registered products for pathogen control
In commercial cleaning, disinfection is a critical step for maintaining healthy environments. EPA-registered disinfectants are essential for ensuring effective pathogen control. These products are rigorously tested and proven to kill specific microorganisms when used as directed.
When selecting disinfectants, it's important to consider factors such as contact time (the time the product needs to remain wet on a surface to be effective), the range of pathogens it targets, and any safety precautions required during use. Many commercial cleaning operations now use quaternary ammonium compounds or hydrogen peroxide-based disinfectants due to their broad-spectrum efficacy and relatively low toxicity.
Specialized surface cleaners: stone, glass, and stainless steel solutions
Different surfaces require specialized cleaning solutions to maintain their appearance and integrity. Stone cleaners, for example, are formulated to clean natural stone surfaces without etching or damaging the material. These products often have a neutral pH and may contain sealants to protect the stone.
Glass cleaners are designed to leave a streak-free finish and often contain alcohol or ammonia to cut through grime and evaporate quickly. For stainless steel surfaces, cleaners with mild abrasives or citrus-based solvents can effectively remove fingerprints and smudges without scratching the surface.
Green cleaning products: Eco-Friendly alternatives and certifications
The demand for environmentally friendly cleaning solutions has led to a surge in green cleaning products. These eco-friendly alternatives are formulated to be biodegradable, non-toxic, and made from renewable resources. Look for certifications such as Green Seal, EcoLogo, or the EPA's Safer Choice label to ensure the products meet strict environmental and performance standards.
Green cleaning products often use plant-based ingredients and avoid harsh chemicals like phosphates, chlorine, or artificial fragrances. While they may require slightly different application methods or longer dwell times compared to traditional chemicals, they can be just as effective when used correctly.
Personal protective equipment (PPE) for commercial cleaning safety
Ensuring the safety of cleaning staff is paramount in commercial cleaning operations. Personal Protective Equipment (PPE) plays a crucial role in protecting workers from potential hazards associated with cleaning chemicals and tasks. Let's explore the essential PPE items that should be part of every commercial cleaning toolkit.
Respiratory protection: N95 masks and powered Air-Purifying respirators
Respiratory protection is critical when working with cleaning chemicals or in dusty environments. N95 masks are commonly used in cleaning operations as they filter out 95% of airborne particles. These masks are effective for most cleaning tasks involving dust or mild chemical exposure.
For more intense cleaning situations or when working with stronger chemicals, Powered Air-Purifying Respirators (PAPRs) offer a higher level of protection. PAPRs use a battery-powered blower to force air through a filter, providing a continuous supply of clean air to the user. While more expensive, PAPRs are particularly useful in environments with poor ventilation or when working with highly volatile chemicals.
Hand and skin protection: Chemical-Resistant gloves and barrier creams
Protecting the hands and skin from chemical exposure is essential in commercial cleaning. Chemical-resistant gloves made from materials like nitrile, neoprene, or butyl rubber provide a barrier against many common cleaning agents. It's important to choose gloves based on the specific chemicals being used, as different materials offer varying levels of protection against different substances.
Barrier creams can provide an additional layer of protection for the skin. These creams create a thin, protective film on the skin that helps prevent irritation from chemicals and makes cleaning up easier at the end of a shift. However, it's important to note that barrier creams are not a substitute for proper gloves and should be used in conjunction with other PPE.
Eye and face protection: safety goggles and face shields
Eye protection is crucial when working with cleaning chemicals or in environments where splashing or airborne particles are a concern. Safety goggles provide a sealed barrier around the eyes, protecting against both liquid splashes and airborne particles. For tasks that involve a higher risk of splashing or when working overhead, full face shields offer additional protection for the entire face.
It's important to ensure that eye protection is comfortable and fits well, as ill-fitting PPE may be removed or adjusted improperly during use, reducing its effectiveness. Many modern safety goggles are designed with anti-fog coatings and ventilation systems to improve comfort during extended wear.
Efficient cleaning tools and accessories for Large-Scale operations
In addition to high-tech equipment and specialized chemicals, efficient cleaning tools and accessories are essential for streamlining large-scale cleaning operations. These tools can significantly enhance productivity and ensure consistent results across various cleaning tasks.
Microfiber technology: mops, cloths, and dusting tools
Microfiber technology has revolutionized the cleaning industry with its superior cleaning performance and durability. Microfiber mops, cloths, and dusting tools are composed of ultra-fine fibers (typically less than 1 denier) that can trap dust, dirt, and even bacteria more effectively than traditional materials.
Microfiber mops can reduce water and chemical usage by up to 95% compared to traditional mops, while still providing superior cleaning results. These mops are available in various styles, including flat mops for large surface areas and string mops for more textured floors. Microfiber cloths are equally versatile, with different weaves and textures designed for specific tasks such as glass cleaning, dusting, or scrubbing.
Telescopic poles and extension wands for High-Reach cleaning
Telescopic poles and extension wands are invaluable tools for accessing high or hard-to-reach areas safely and efficiently. These tools can extend a cleaner's reach by several feet, eliminating the need for ladders in many situations and reducing the risk of falls.
Modern telescopic poles are often made from lightweight materials like carbon fiber or aluminum, making them easy to maneuver. They can be fitted with a variety of attachments such as dusters, squeegees, or even small scrub brushes, allowing cleaners to tackle a wide range of high-reach cleaning tasks without changing tools.
Ergonomic cleaning carts and caddies for organized supply management
Well-designed cleaning carts and caddies are essential for organizing supplies and improving workflow efficiency. Ergonomic carts feature compartments for different cleaning tools, chemicals, and waste collection, allowing cleaners to have everything they need at hand as they move through a facility.
Many modern cleaning carts incorporate features like adjustable shelves, locking cabinets for chemical storage, and even built-in wringer systems for mops. Some advanced models include silent casters for quiet operation in noise-sensitive environments like hospitals or libraries.
Advanced cleaning technologies for specialized environments
As cleaning technology continues to evolve, new advanced solutions are emerging to address the unique challenges of specialized environments. These cutting-edge technologies offer improved efficiency, effectiveness, and safety in commercial cleaning operations.
Electrostatic sprayers for uniform disinfectant application
Electrostatic sprayers have gained significant popularity, especially in light of recent public health concerns. These devices apply an electric charge to disinfectant solutions as they are sprayed, causing the droplets to be attracted to surfaces and wrap around them for more complete coverage.
The technology allows for rapid application of disinfectants, with some models capable of treating up to 18,000 square feet per hour. This makes electrostatic spraying particularly useful in large facilities or areas that require frequent disinfection, such as schools, gyms, or public transportation.
UV-C light disinfection systems for healthcare facilities
UV-C light disinfection systems use short-wavelength ultraviolet light to kill or inactivate microorganisms by destroying their DNA. These systems are particularly valuable in healthcare settings where thorough disinfection is critical.
Portable UV-C units can be moved from room to room, disinfecting surfaces and air in a matter of minutes without the use of chemicals. Some advanced systems combine UV-C technology with mapping capabilities to ensure complete coverage of a space. While effective, it's important to note that UV-C light can be harmful to humans, so proper safety protocols must be followed during use.
Dry ice blasting equipment for industrial decontamination
Dry ice blasting is an innovative cleaning method that uses pellets of solid carbon dioxide (dry ice) propelled at high speeds to clean surfaces. As the dry ice pellets hit the surface, they sublimate from solid to gas, expanding rapidly and dislodging contaminants without leaving any residue.
This technology is particularly useful for industrial cleaning tasks such as removing grease from machinery, stripping paint, or cleaning electrical components. Dry ice blasting is non-abrasive, non-conductive, and doesn't introduce moisture, making it safe for use on sensitive equipment. It's also environmentally friendly, as it doesn't generate secondary waste streams.
Maintenance and storage solutions for cleaning equipment longevity
Proper maintenance and storage of cleaning equipment and supplies are crucial for ensuring their longevity and optimal performance. Implementing effective maintenance protocols can significantly reduce downtime and replacement costs while ensuring consistent cleaning results.
Equipment cleaning protocols: daily, weekly, and monthly procedures
Establishing a structured cleaning and maintenance schedule for equipment is essential. Daily procedures might include tasks like emptying and cleaning vacuum bags or canisters, wiping down machine exteriors, and checking for any visible damage. Weekly maintenance could involve more thorough cleaning of components, such as washing or replacing filters and inspecting power cords for wear.
Monthly or quarterly maintenance procedures should be more comprehensive, potentially including tasks like lubricating moving parts, deep cleaning of internal components, and professional servicing of complex machinery. Keeping detailed maintenance logs can help track the condition of equipment over time and anticipate when replacements or repairs might be needed.
Proper chemical storage: OSHA guidelines and safety data sheets (SDS)
Adhering to proper chemical storage practices is crucial for safety and compliance. The Occupational Safety and Health Administration (OSHA) provides guidelines for the safe storage of cleaning chemicals, including requirements for ventilation, containment of spills, and separation of incompatible substances.
Safety Data Sheets (SDS) for each chemical should be readily available and easily accessible to all staff. These documents provide crucial information about the properties of each chemical, potential hazards, and proper handling procedures. Implementing a color-coding system for chemical storage areas and ensuring all containers are clearly labeled can help prevent accidents and improve efficiency.
Equipment repair and replacement: preventative maintenance schedules
Implementing a preventative maintenance schedule can help identify and address potential issues before they lead to equipment failure. This might include regular professional servicing of complex machinery, replacing wear parts at recommended intervals, and conducting routine performance checks.
When equipment does require repair, it's important to use authorized service providers and genuine replacement parts to maintain performance and safety standards. Keeping detailed records of repairs and part replacements can help inform decisions about when it's more cost-effective to replace rather than repair aging equipment.
By implementing these comprehensive strategies for equipment, supplies, and maintenance, commercial cleaning operations can ensure they are well-equipped to meet the diverse challenges of modern cleaning environments. From cutting-edge technologies to fundamental safety practices, each element plays a crucial role in delivering efficient, effective, and safe
cleaning environments. Proper maintenance and storage not only extend the life of your equipment and supplies but also ensure they perform at their best when needed.
Equipment cleaning protocols: daily, weekly, and monthly procedures
Implementing a structured cleaning and maintenance schedule for equipment is crucial for optimal performance and longevity. Daily procedures should include tasks like emptying and cleaning vacuum bags or canisters, wiping down machine exteriors, and checking for any visible damage. This regular attention helps prevent the buildup of dirt and debris that can impair equipment function.
Weekly maintenance might involve more thorough cleaning of components, such as washing or replacing filters and inspecting power cords for wear. For example, floor scrubbers may require a deep clean of the brushes and squeegees to prevent residue buildup and ensure consistent cleaning results.
Monthly or quarterly maintenance procedures should be more comprehensive. These might include tasks like lubricating moving parts, deep cleaning of internal components, and professional servicing of complex machinery. For instance, carpet extractors may need descaling of heating elements and thorough cleaning of solution tanks to prevent bacterial growth.
Keeping detailed maintenance logs is essential. These records help track the condition of equipment over time and anticipate when replacements or repairs might be needed. Digital maintenance tracking systems can streamline this process, providing automated reminders and detailed service histories for each piece of equipment.
Proper chemical storage: OSHA guidelines and safety data sheets (SDS)
Adhering to proper chemical storage practices is crucial for safety and compliance in commercial cleaning operations. The Occupational Safety and Health Administration (OSHA) provides comprehensive guidelines for the safe storage of cleaning chemicals. These include requirements for proper ventilation to prevent the buildup of harmful fumes, containment measures for potential spills, and the separation of incompatible substances to avoid dangerous reactions.
Safety Data Sheets (SDS) for each chemical should be readily available and easily accessible to all staff. These documents provide crucial information about the properties of each chemical, potential hazards, and proper handling procedures. In case of an accident or spill, quick access to SDS can be critical for appropriate response and treatment.
Implementing a color-coding system for chemical storage areas can significantly improve safety and efficiency. For example, you might use red labels for flammable substances, blue for corrosives, and green for eco-friendly products. Ensuring all containers are clearly labeled with their contents, hazard warnings, and expiration dates is also essential for maintaining a safe working environment.
Equipment repair and replacement: preventative maintenance schedules
Implementing a preventative maintenance schedule is key to identifying and addressing potential issues before they lead to equipment failure. This proactive approach can significantly reduce downtime and extend the lifespan of your cleaning equipment. For example, vacuum motors might be scheduled for inspection every 500 hours of use, while floor scrubber brushes may need replacement after a certain square footage of cleaning.
When equipment does require repair, it's important to use authorized service providers and genuine replacement parts to maintain performance and safety standards. While third-party parts may seem cost-effective in the short term, they can often lead to reduced efficiency and potential safety risks.
Keeping detailed records of repairs and part replacements is invaluable for making informed decisions about equipment lifecycle management. These records can help identify patterns of wear or failure, informing decisions about when it's more cost-effective to replace rather than repair aging equipment. For instance, if a particular model of vacuum cleaner consistently requires motor replacement after two years of use, it might be more economical to upgrade to a more durable model.